Grind away: How mechanochemistry could revolutionize materials
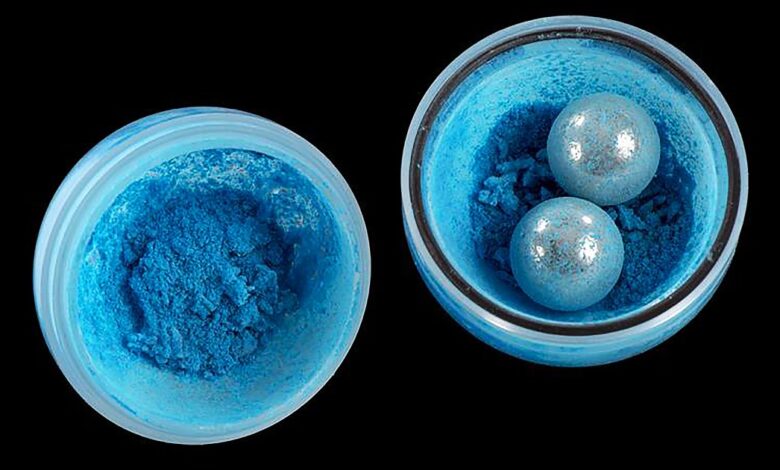
Sign up for the Smarter Faster newsletter
A weekly newsletter featuring the biggest ideas from the smartest people
The archetypal image of chemistry is a set of glassware, full of colorful liquids about to be mixed. Froth, bubbles, and smoke ensue. Much of industrial chemical synthesis is a tamer version of this. But could we replace the bubbling flask with the slow grind of a ball mill? A scientific review article details progress in the field of mechanochemistry, investigating this question.
When chemists start grinding
Most traditional chemical syntheses rely on random thermal motion driven by mixing to bring reactants together. Solvents dissolve materials into fluid form, and the dissolved materials are comingled, stirred, heated, filtered, and distilled to create and isolate new compounds. Electrochemical synthesis drives a reaction with an electrical current. Electrolysis of water to liberate hydrogen and oxygen is one example. Photochemistry uses light to drive reactions, with photosynthesis being an abundant natural demonstration. The breakdown of plastic under prolonged sunlight is another. (Nanofabrication, if it is possible, would synthesize molecules by using tiny machines to pluck atoms out of bins and poke them together.)
Mechanochemistry, by contrast, uses mechanical force to combine reactants. A simple form of mechanochemistry is grinding reactants with a mortar and pestle until a product forms in the pestle. Simple studies have found that many compounds can be synthesized by human hands without resorting to liquid solutions and solvents.
Grinding is more efficient when performed with an instrument called a ball mill, which grinds down a substance into a fine powder. The simplest ball mill consists of a cylindrical reaction vessel mounted on its side and spun around its central axis. The vessel is a jar filled with powdered chemical reactants and a number of hard balls. In some cases, additional liquid or salt compounds are added to catalyze the reaction. As a motor rotates the vessel, the balls roll up the vessel wall and then fall back down onto the other balls in the chemical mixture. Each ball-on-ball strike crushes and mixes small amounts of powder at the strike point. In this way, the rotation and colliding balls churn the materials.
There are other ways to grind. The jar can be stood upright and shaken side-to-side at certain frequencies. A more powerful and industrially scalable method is to spin the jar about its central axis while also rolling it along the inside of a larger cylinder. This can rotate the jar rapidly enough to throw the balls and mixture back and forth with more force than gravity alone could impart. It’s a bit like putting a brick in a laundry machine. (Don’t try this at home.)
The balls and jars are generally made of the same material, chosen for several reasons. Harder and denser balls, such as stainless steel, tungsten carbide, or agate, grind and smash the material more easily. Polytetrafluorethylene (PTFE), better known by its commercial trademark Teflon, or a clear polymer like polymethylmethacrylate (PMMA) are also used as they clean easily and don’t tend to shed material that contaminates the product. Copper balls and jars also can catalyze reactions, such as cycloaddition.
Mechanochemistry under pressure
The mechanochemistry review paper discusses how various chemical syntheses that were previously performed with solvents can be replicated using solvent-free mechanical grinding methods that are simpler, faster, and cleaner. It also points out that a few rare or entirely new syntheses have been achieved. Why, then, is the technique not standard in industry?
Mechanochemistry, they argue, is still qualitative and intuitive rather than quantitative and precise. Ironically, mechanochemical reactivity is not understood mechanically. For instance, the mechanics vary by the type of stress involved. Effects of normal stress, a head-on pressure felt by a molecule directly smashed between two colliding balls, differ in important ways from those of shear stress, a perpendicular force felt by molecules caught between two balls sliding across one another. Kinetic effects (those described by impacts of rigid bodies) and thermodynamic effects (those involving compression, heating, and energy transmutation) must be separated. The prevalence and importance of localized heating at ball impact locations are also unclear.
To study the reactions, real-time measurements of reactants and products are required. Transparent polymer jars allow a laser to access the contents, performing Raman spectroscopy to fingerprint individual compounds. Some jars efficiently pass X-rays, and the diffraction of the X-rays through the powder identifies the crystalline grains present within it. Measuring the fractions of different molecules present throughout the grind is a crucial way to quantify the dynamics of the reaction and provide data for modeling. Models that consider the particles as a pseudo-fluid may help chemists understand and predict reactions.
New techniques and a better theoretical understanding could encourage the commercialization of mechanochemistry. External factors such as environmental and emissions regulations may provide additional incentives. However, while it may be possible to replace bubbling flasks with ball mills, we don’t yet fully know how.
Sign up for the Smarter Faster newsletter
A weekly newsletter featuring the biggest ideas from the smartest people